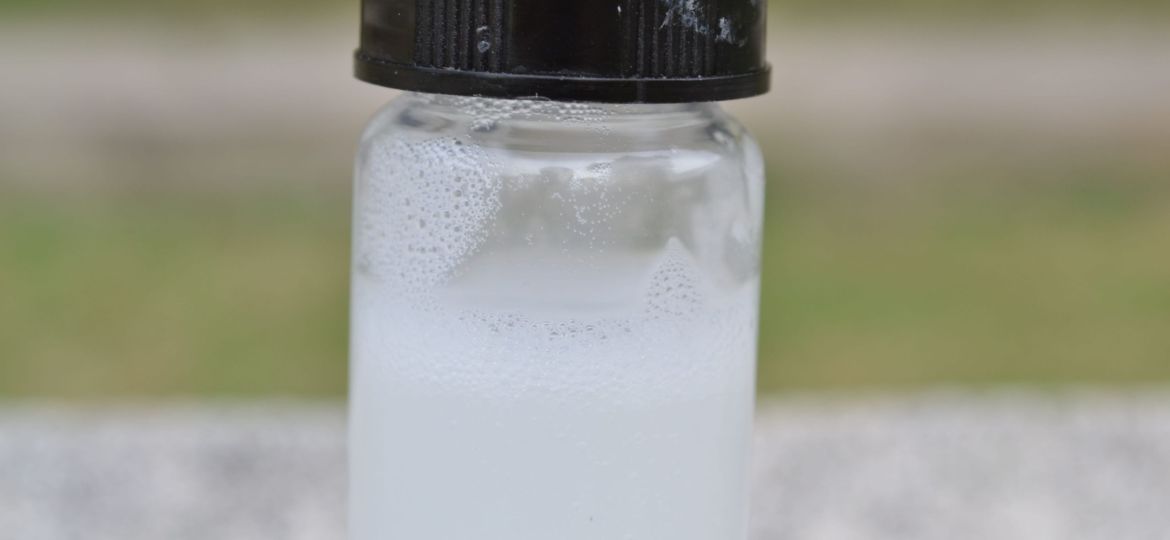
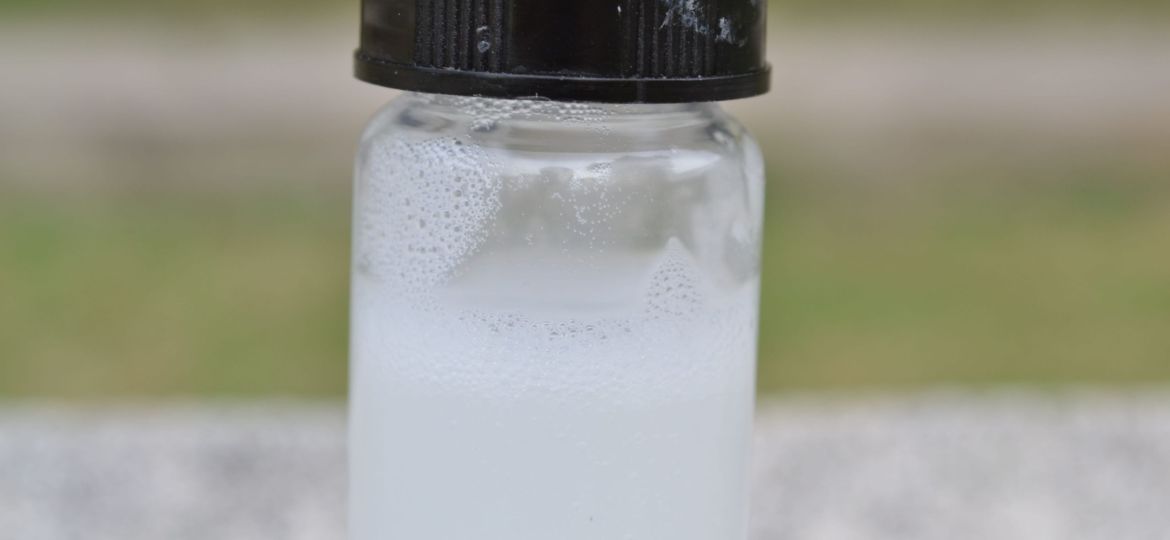
“Explore our latest blog post on green technology and eco-friendly polyurethanes. These innovative polymers provide exceptional durability, flexibility, and resistance, ideal for various industrial and consumer applications. By choosing eco-friendly polyurethanes, you contribute to reducing environmental impact while enjoying superior performance. Learn how these sustainable solutions are paving the way for a greener future in materials science and technology. Discover cutting-edge advancements and real-world applications that showcase the transformative potential of eco-friendly polyurethanes. Join us in embracing a sustainable approach to modern materials.”
- Eco-friendly
- High Solid
- Single Component
- Chemical & Impact Resistant
- Water-proofing
- Affordable Price
Polymeric Coatings: Advanced Applications and Surface Modification
Surface modification has become a highly attractive research area in recent times, driven by the demand for materials with well-defined surface properties. The aim is to meet specific requirements that enhance the value and functionality of materials in various technological applications. Surface modification can be simplified as a process that introduces new surface behaviors to materials, fulfilling desirable requirements. These modifications often result in new morphological features that affect how the material interacts with its environment.
Historically, surface modification has been used for many years, dating back to ancient times. Early examples include protecting metallic tools with materials like clay, vegetable oils, gelatins, beeswax, and animal fats. These coatings provided properties such as corrosion protection, gloss, wear resistance, water repellence, and lubrication.
Today, the theory and application of surface modification through coatings have evolved significantly. Polymeric, inorganic, and hybrid coatings can be tailored to perform specific functions in numerous applications. Examples include coatings on laptops, mobile phones, home furniture, cars, solar cell panels, orthopedic implants, medical devices, radars, aircraft, satellites, and invisible paints. Polymeric coatings, in particular, have gained significant attention and are expected to continue rising in importance in the coming years.
Polymeric coatings are of outstanding interest due to their versatility and desirable properties, such as thermal barrier, hydrophilic/hydrophobic balance, anti-fouling, fire retardant, corrosion protection, anti-microbial, self-cleaning, hardness, wear resistance, lubrication, abrasion resistance, photocatalytic activity, photochromic behavior, photoluminescence, anti-reflection, electromagnetic properties, antistatic behavior, dielectric properties, insulating capabilities, conductivity, and shielding.
Waterborne Polyurethane Dispersion (PUD)
The synthesis of polymeric coatings, paints, and inks often faces challenges due to the evaporation of volatile organic compounds (VOC). To mitigate environmental impact, regulatory bodies like the Environmental Protection Agency (EPA) have set restrictions on VOC use, promoting the development of low-VOC or environmentally friendly materials. Water has emerged as an excellent choice for preparing low-VOC coating systems.
Waterborne polyurethane dispersions (PUDs) are highly suitable for industrial applications due to their outstanding properties, including chemical resistance, solvent resistance, abrasion resistance, flexibility, hardness, elasticity, and suitability for a broad range of substrates. PUDs have found applications in primers for various metals, adhesives, coatings, foam industries, elastomers, paints, and textiles.
PUDs belong to a versatile class of colloidal dispersion systems. Their performance and properties strongly depend on physico-chemical interactions and interfacial forces. Stable colloidal dispersions are achieved when the discontinuous phase (droplets) is uniformly distributed in the continuous phase (liquid medium). Instability occurs when droplets aggregate, leading to a decrease in total surface area.
Basis Chemistry of Polyurethane
Polyurethanes are alternating segmented polymers comprising soft and hard segments with micro-phase separation. These polymers can incorporate ions to produce polyurethane ionomers with innovative properties. The preparation and characterization of various PU ionomers have been extensively researched. Polyurethane ionomer dispersions are created by dispersing amphiphilic pre-polymers using soft segments (polyols), hard segments (diisocyanates), and internal emulsifiers like dimethylolpropionic acid, followed by a chain extension step.
The interaction of polar urethane groups via hydrogen bonding and low polar segments contributes to the desirable properties and performance of PUDs. By varying the soft segments’ molecular weights and the ratio of hard to soft segments (NCO to OH ratio), different types of materials can be obtained, ranging from brittle and hard to tacky and soft.
Hard Segment (Polyfunctional Isocyanate)
Various types of hard segments (polyfunctional isocyanates) are available for PU synthesis, including aliphatic, cycloaliphatic, polycyclic, or aromatic isocyanates. The choice of hard segment significantly impacts the performance and properties of the resulting PU coatings. For example, aliphatic hard segments like Isophoron diisocyanate (IPDI) or hexamethylene diisocyanate (HDI) offer good UV stability, scratch resistance, and gloss properties. In contrast, aromatic hard segments like Toluene diisocyanate (TDI) or Methylene diphenyl diisocyanate (MDI) provide rigidity but lower UV and oxidative stability.
Reactions of Hard Segment (Polyfunctional Isocyanate)
Polyfunctional isocyanates are highly reactive with hydrogen-containing compounds, leading to various important reactions:
- Reaction with Alcohols (R-OH): An exothermic reaction essential in PU synthesis, generating urethane groups.
- Reaction with Water (H2O): Produces carbon dioxide and urea groups, convenient for PU foam production.
- Reaction with Urethanes: Forms allophanates at high temperatures, contributing to cross-linking.
- Reaction with Urea: Forms biuret, another cross-linking source at high temperatures.
- Reaction with Carboxylic Acids: Less reactive but forms amine products.
- Reaction with Epoxides: Produces oxazolidones in the presence of specific catalysts.
- Reaction with Cyclic Anhydrides: Produces cyclic imides.
- Dimerization of Polyfunctional Isocyanate: Produces carbodiimides and uretidinediones.
- Trimerization of Polyfunctional Isocyanate: Produces isocyanurates, which are stable and water-dispersible.
Soft Segment (Polyol)
Various types of soft segments (polyols) are used in PU synthesis, including polycaprolactone (PCL), polyester polyols, polyether polyols, polycarbonate polyols, and natural oil-based polyols. The choice of soft segment affects the resulting PU’s properties, such as flexibility, hardness, thermal stability, and chemical resistance. For example, polyester polyols provide excellent heat stabilization and oil resistance, while polyether polyols offer flexibility and low-temperature performance.
Catalysts in PU Synthesis
Catalysts accelerate the rate of PU reactions at lower temperatures. They are classified into tertiary amines and organometallic compounds. The catalytic activity depends on electronic and steric effects. Tertiary amines like triethylamine (TEA) and triethylenediamine (TEDA) are strong catalysts, while organometallic complexes like stannous octoate and dibutyltin dilaurate (DBTDL) are commonly used. Catalysts impact the reactivity and order of reactions, affecting the final PU properties.
Classification of PU Coatings
According to ASTM-D16-00, polyurethane coatings are classified into six categories, each with distinct characteristics and curing mechanisms:
- Type-I (1K) (pre-reacted): Unsaturated drying oil with no free NCO, cured by drying oil oxidation.
- Type-II (1K) (moisture cured): NCO terminated, cured by reaction with air moisture.
- Type-III (1K) (heat cured): Blocked NCO, cured by heating.
- Type-IV (2K) (catalyst): NCO pre-polymer with catalyst, cured by reaction with moisture.
- Type-V (2K) (polyol): Two components (NCO and hydroxyl), cured by reaction between components.
- Type-VI (2K) (nonreactive lacquer): Completely polymerizes PU dissolved in a solvent, cured by solvent evaporation.
Waterborne Polyurethane Dispersion (PUD): Advanced Applications and Characteristics
The shift towards environmentally friendly materials has driven significant research in developing low-VOC technologies. Among these, waterborne polyurethane dispersions (PUDs) have emerged as a highly suitable solution for various industrial applications. These dispersions offer exceptional properties such as chemical resistance, abrasion resistance, flexibility, hardness, elasticity, and suitability for a broad range of substrates. PUDs are now used in primers for metals, adhesives, coatings, foam industries, elastomers, paints, and textiles.
PUDs are a versatile class of colloidal dispersion systems. Their performance and properties are strongly dependent on physico-chemical interactions and interfacial forces. Stable colloidal dispersions are achieved when the discontinuous phase (droplets) is uniformly distributed in the continuous phase (liquid medium). Instability occurs when droplets aggregate, leading to a decrease in total surface area.
Basis Chemistry of Polyurethane
Polyurethanes are alternating segmented polymers comprising soft and hard segments with micro-phase separation. These polymers can incorporate ions to produce polyurethane ionomers with innovative properties. The preparation and characterization of various PU ionomers have been extensively researched. Polyurethane ionomer dispersions are created by dispersing amphiphilic pre-polymers using soft segments (polyols), hard segments (diisocyanates), and internal emulsifiers like dimethylolpropionic acid, followed by a chain extension step.
The interaction of polar urethane groups via hydrogen bonding and low polar segments contributes to the desirable properties and performance of PUDs. By varying the soft segments’ molecular weights and the ratio of hard to soft segments (NCO to OH ratio), different types of materials can be obtained, ranging from brittle and hard to tacky and soft.
Hard Segment (Polyfunctional Isocyanate)
Various types of hard segments (polyfunctional isocyanates) are available for PU synthesis, including aliphatic, cycloaliphatic, polycyclic, or aromatic isocyanates. The choice of hard segment significantly impacts the performance and properties of the resulting PU coatings. For example, aliphatic hard segments like Isophoron diisocyanate (IPDI) or hexamethylene diisocyanate (HDI) offer good UV stability, scratch resistance, and gloss properties. In contrast, aromatic hard segments like Toluene diisocyanate (TDI) or Methylene diphenyl diisocyanate (MDI) provide rigidity but lower UV and oxidative stability.
Reactions of Hard Segment (Polyfunctional Isocyanate)
Polyfunctional isocyanates are highly reactive with hydrogen-containing compounds, leading to various important reactions:
- Reaction with Alcohols (R-OH): An exothermic reaction essential in PU synthesis, generating urethane groups.
- Reaction with Water (H2O): Produces carbon dioxide and urea groups, convenient for PU foam production.
- Reaction with Urethanes: Forms allophanates at high temperatures, contributing to cross-linking.
- Reaction with Urea: Forms biuret, another cross-linking source at high temperatures.
- Reaction with Carboxylic Acids: Less reactive but forms amine products.
- Reaction with Epoxides: Produces oxazolidones in the presence of specific catalysts.
- Reaction with Cyclic Anhydrides: Produces cyclic imides.
- Dimerization of Polyfunctional Isocyanate: Produces carbodiimides and uretidinediones.
- Trimerization of Polyfunctional Isocyanate: Produces isocyanurates, which are stable and water-dispersible.
Soft Segment (Polyol)
Various types of soft segments (polyols) are used in PU synthesis, including polycaprolactone (PCL), polyester polyols, polyether polyols, polycarbonate polyols, and natural oil-based polyols. The choice of soft segment affects the resulting PU’s properties, such as flexibility, hardness, thermal stability, and chemical resistance. For example, polyester polyols provide excellent heat stabilization and oil resistance, while polyether polyols offer flexibility and low-temperature performance.
Catalysts in PU Synthesis
Catalysts accelerate the rate of PU reactions at lower temperatures. They are classified into tertiary amines and organometallic compounds. The catalytic activity depends on electronic and steric effects. Tertiary amines like triethylamine (TEA) and triethylenediamine (TEDA) are strong catalysts, while organometallic complexes like stannous octoate and dibutyltin dilaurate (DBTDL) are commonly used. Catalysts impact the reactivity and order of reactions, affecting the final PU properties.
Classification of PU Coatings
According to ASTM-D16-00, polyurethane coatings are classified into six categories, each with distinct characteristics and curing mechanisms:
- Type-I (1K) (pre-reacted): Unsaturated drying oil with no free NCO, cured by drying oil oxidation.
- Type-II (1K) (moisture cured): NCO terminated, cured by reaction with air moisture.
- Type-III (1K) (heat cured): Blocked NCO, cured by heating.
- Type-IV (2K) (catalyst): NCO pre-polymer with catalyst, cured by reaction with moisture.
- Type-V (2K) (polyol): Two components (NCO and hydroxyl), cured by reaction between components.
- Type-VI (2K) (nonreactive lacquer): Completely polymerizes PU dissolved in a solvent, cured by solvent evaporation.
Research and Development in PUD
Significant research has been conducted on waterborne polyurethane dispersions and their applications. Researchers have explored various combinations of diacids, polyols, and chain extenders to enhance the performance and properties of PUDs. For example, Vilas D. Athawale and Mona A. Kulkarni synthesized environmentally friendly PUDs using combinations of adipic acid, maleic anhydride, and isophthalic acid with trimethylolpropane (TMP) and neopentyl glycol (NPG). Their work showed that hybrid systems of polyurethane/acrylate offered excellent chemical resistance, thermal stability, hardness, colloidal stability, and glass transition temperature (Tg). Aamer Saeed and Ghulam Sabir developed high gloss and thermally stable PUD/PAC resins using polyethylene glycol (PEG) and hexamethylene diisocyanate (HDI). They used pre-polymer techniques and introduced double bond functionality to make water-dispersible resins. Their research concluded that synthesized high gloss resins have superior properties for commercial applications. Vilas et al. also prepared hybrid systems of PUD with acrylic monomers, demonstrating better chemical and mechanical resistance compared to simple physical blends. Their work highlighted the compatibility and homogeneous morphology of the hybrid systems. Pablo et al. synthesized pure PUDs and hybrid composites with varying compositions, showing non-linear behavior with increased acrylic content in hybrid systems. Their studies included comprehensive characterizations such as FTIR, TEM, UV, SEC, AFM, DLS, WAXS/SAXS, gel content measurements, mechanical properties analysis, pencil hardness, water contact angle, and surface roughness. Aznar et al. developed glossy topcoat paints using pure PUD and PUD/AC hybrid resins. Their standardized tests indicated that hybrid system-based paints exhibited higher gloss and optical properties than those prepared with pure PUD resin. V.V. Gite et al. investigated the effect of isocyanate to hydroxyl ratio and the properties of polyurethane coatings prepared with acrylic polyol and trimerized IPDI. Their results showed that higher NCO to OH ratio resulted in more tensile strength and hardness, while lower ratio increased elongation. Li et al. successfully synthesized PUDs with 50% solid content using aliphatic isocyanate IPDI and varying polyol molecular weights. They found that particle size decreased with increased internal emulsifier concentration and specific NCO to OH ratios. Aruna and Kumar synthesized eco-friendly PUDs tested for leather and footwear industries, showing superior adhesive properties and excellent peel and shear strengths for leather bonding. Rahman and Kim studied the adhesive behavior and various properties of PUDs, finding that stable dispersions were achieved with specific DMPA content and that increased DMPA concentration led to decreased particle size and increased viscosity. Wei and Xin prepared anionic PUDs using different isocyanates, demonstrating stable colloidal dispersions with nano-sized particles. They concluded that higher HDI content improved hydrophilic efficiency and decreased coating hardness. Bao et al. synthesized PUDs using natural oil-based polyols, showing improved hydrolytic stability and mechanical properties with specific soft segments. Lee et al. reported the synthesis of anionic PUDs with polycarbonate diol of different molecular weights, finding that lower molecular weight led to smaller particle sizes. Environmentally friendly poly(urethane-imide) was synthesized to enhance the processability and reduce solvent emissions, showing improved thermal stability with imide incorporation.
Synthesis Techniques of PUD
Several techniques are used for synthesizing PUDs:
- Pre-polymer Process: Involves reacting an oligo-polyol with diisocyanate to form NCO-terminated pre-polymers, followed by chain extension.
- Quasi-prepolymer Process: Similar to the pre-polymer process but with an excess of isocyanate, resulting in a mixture of free isocyanates and pre-polymers.
- One Shot Process: A single-step process involving the efficient mixing of all raw materials, including isocyanate, polyol, catalysts, chain extender, and other auxiliaries.
- Acetone Process: Involves adding acetone to facilitate processing, followed by neutralization, dispersion in water, and acetone evaporation.
Experimental Techniques
- Fourier Transform Infrared (FTIR) Spectroscopy: Used to identify functional groups and analyze molecular absorption and transmission.
- Rheological Measurements: Evaluate deformation and flow behavior, viscosity, and other rheological properties of PUDs.
Conclusion
Waterborne polyurethane dispersions (PUDs) represent a significant advancement in environmentally friendly coating technologies. Their versatile applications, excellent properties, and compliance with regulatory standards make them highly desirable for various industrial uses. Ongoing research and development continue to enhance their performance, making PUDs a key component in the future of polymeric coatings.
For more information on our high-quality advanced Polyurethane Coatings, please visit our Polyurethane Coating product page.
"Embrace sustainability with eco-friendly polyurethanes — innovative solutions that enhance durability and performance while protecting our planet for future generations."