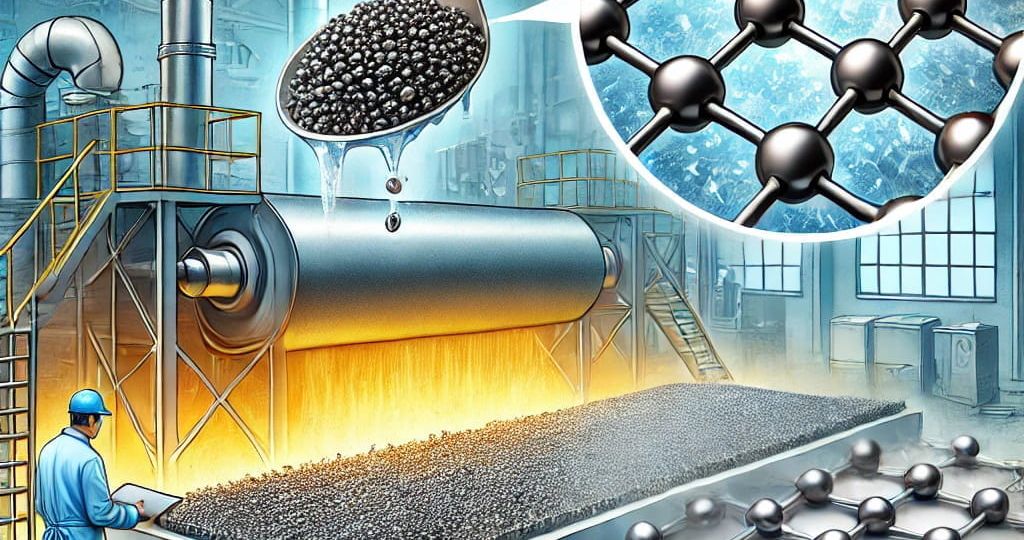
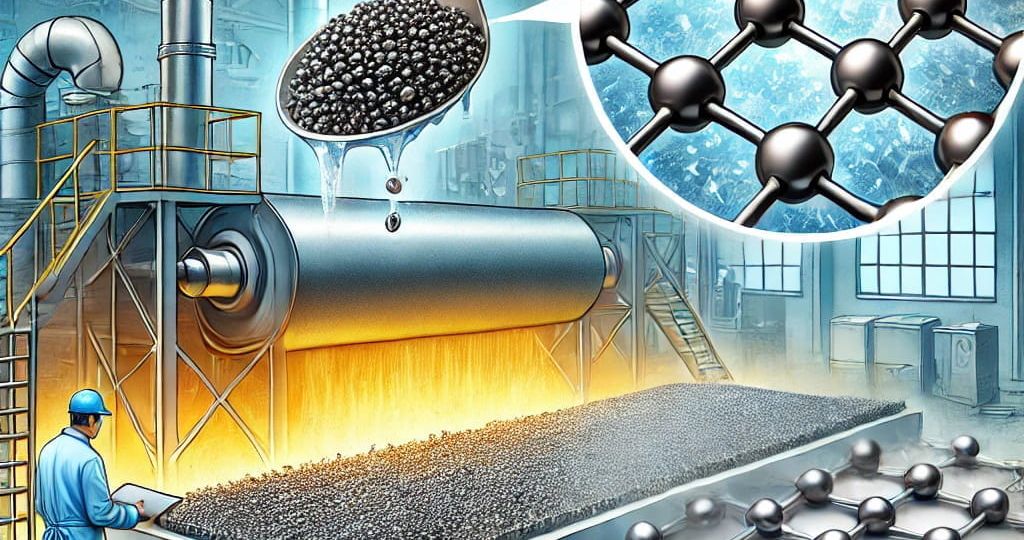
Abstract
This study presents a detailed examination of Graphene and Nanoparticle-Enhanced Cold Galvanizing Compounds (CGCs) to provide superior corrosion protection for metallic structures. The research explores the electrochemical, morphological, and mechanical properties of these advanced formulations, demonstrating significant improvements in their performance. The findings highlight the potential of these Graphene and Nanoparticle-Enhanced CGCs in extending the lifespan of metallic infrastructure, particularly in harsh environments. Recent advancements in Graphene and Nanoparticle-Enhanced Cold Galvanizing Compounds show promising results for future applications in industrial settings.
Introduction to Graphene and Nanoparticle-Enhanced Cold Galvanizing Compounds
Corrosion poses a significant challenge across industries, particularly those reliant on metals. Traditional methods like painting, hot-dip galvanizing, and the use of corrosion inhibitors have limitations, especially in terms of long-term protection and environmental impact. These methods often fall short in providing durable, effective protection, leading to the premature degradation of metal structures.
Graphene and Nanoparticle-Enhanced Cold Galvanizing Compounds (CGCs) offer an effective alternative by forming a protective barrier that shields the metal from corrosive elements. These compounds typically contain a high concentration of zinc, which acts as a sacrificial anode, corroding in place of the underlying metal. This process, known as galvanic protection, is crucial for extending the life of metal structures.
Recent advancements in nanotechnology have opened new avenues for enhancing the performance of Graphene and Nanoparticle-Enhanced CGCs. By incorporating nanoparticles such as nanolayered graphene (NGr) and red iron oxide (Fe2O3) into Graphene and Nanoparticle-Enhanced CGCs, it is possible to significantly improve their electrochemical properties, mechanical strength, and overall durability. This study explores the use of these nanoparticles to develop advanced Graphene and Nanoparticle-Enhanced Cold Galvanizing Compounds that offer superior corrosion protection, even under harsh environmental conditions.
Materials and Methods for Developing Graphene-Enhanced Cold Galvanizing Compounds
The research focuses on Graphene and Nanoparticle-Enhanced Cold Galvanizing Compounds (CGCs) using a polymer matrix, zinc dust, and nanoparticles like NGr and Fe2O3. Various concentrations of these nanoparticles were tested to assess their impact on the corrosion resistance, surface morphology, and mechanical properties of Graphene and Nanoparticle-Enhanced CGCs. Electrochemical impedance spectroscopy (EIS) and polarization measurements were employed to evaluate the electrochemical properties of the formulations. Additionally, field-emission scanning electron microscopy (FE-SEM) was used to observe the distribution of nanoparticles within the Graphene-Enhanced CGC matrix.
Results and Discussion on Graphene and Nanoparticle-Enhanced Cold Galvanizing Compounds
Surface Morphology of Graphene-Enhanced Cold Galvanizing Compounds
The surface morphology of the Graphene and Nanoparticle-Enhanced CGCs was analyzed using FE-SEM. The results revealed a uniform distribution of NGr and Fe2O3 nanoparticles within the Graphene-Enhanced CGC matrix, which is crucial for ensuring consistent protection across the metal surface. The nanoparticles effectively filled the voids between the zinc particles, reducing the porosity of the coating and increasing its density, essential for preventing the ingress of corrosive elements.
Corrosion Potential in Graphene and Nanoparticle-Enhanced Galvanizing Compounds
Corrosion potential measurements demonstrated that the incorporation of NGr and Fe2O3 nanoparticles significantly lowered the corrosion potential of the coatings, indicating improved cathodic protection. The lower corrosion potential suggests that the nanoparticles enhance the electrochemical activity of the zinc, allowing it to more effectively protect the underlying metal. This improvement was particularly notable at reduced pigment volume concentrations (PVCs), demonstrating that the use of nanoparticles can reduce the overall amount of zinc required without compromising the protective performance.
Electrochemical Analysis of Nanoparticle-Enhanced Galvanizing Compounds
Electrochemical impedance spectroscopy (EIS) results showed that the incorporation of NGr and Fe2O3 nanoparticles led to a significant increase in the impedance of the coatings. This increase in impedance indicates enhanced barrier properties, which prevent the penetration of corrosive species. The nanoparticles contribute to the formation of a more compact and homogeneous coating, less permeable to moisture and salts, resulting in superior long-term protection compared to traditional formulations.
Salt Spray Analysis of Graphene and Nanoparticle-Enhanced Cold Galvanizing Compounds
Salt spray testing was conducted to simulate the harsh conditions that metal structures may encounter in marine and coastal environments. The results demonstrated that the Graphene and Nanoparticle-Enhanced Cold Galvanizing Compounds outperformed traditional coatings in terms of resistance to salt-induced corrosion. The coatings showed minimal signs of rust and maintained their adhesion to the metal surface even after prolonged exposure to the salt spray, indicating that the nanoparticles play a crucial role in reinforcing the protective barrier and extending the lifespan of the coated metal.
Rheology of Graphene and Nanoparticle-Enhanced Galvanizing Compounds
Rheological measurements assessed the flow properties of the Graphene and Nanoparticle-Enhanced Cold Galvanizing Compounds, which are important for their application and performance. The addition of nanoparticles improved the rheological properties of the coatings, making them easier to apply and ensuring a smooth and uniform coating. The enhanced flow characteristics also contributed to the formation of a more consistent coating thickness, essential for achieving optimal protection. The improved rheology of the Graphene and Nanoparticle-Enhanced CGCs ensures they can be applied effectively in various industrial settings, providing reliable corrosion protection.
Conclusion on Graphene and Nanoparticle-Enhanced Galvanizing Compounds
This research demonstrates the potential of Graphene and Nanoparticle-Enhanced Cold Galvanizing Compounds (CGCs) as a superior alternative to traditional corrosion protection methods. The advanced formulations provide enhanced protection against corrosion while reducing the environmental impact associated with high zinc usage. The findings of this study suggest that further exploration of nanotechnology in protective coatings could lead to even more effective solutions for corrosion management.
Explore Our Product: ZRC Paint Cold Galvanizing Compound Roval
For those interested in applying this advanced technology, our ZRC Paint Cold Galvanizing Compound Roval offers all the benefits discussed in this study. This product is designed to provide superior corrosion protection for metallic structures, making it an ideal choice for various industrial applications.
ZRC Paint Cold Galvanizing Compound ROVAL offers exceptional cathodic protection, leveraging zinc’s electrochemical properties to prevent rust and corrosion. This advanced coating forms a galvanic barrier, ensuring long-term durability and reliability. Ideal for various industrial applications, it provides a robust solution for structural steel, enhancing its lifespan even in harsh environments. The self-healing nature of the zinc particles in the compound ensures continuous protection, making it a superior alternative to traditional galvanizing methods.
- Single Component
- Ready-to-use Paint
- Dry Time = 10 Min
- 96% Zinc Content
- Galvanizing with Paint
- 4000+ Hours Salt Spray Test
- 20+ Years Protection
- Hot-dip Galvanizing Alternative